In-Pipe Robotics
“Polaroid 2008: giant pipes going into the roof of one hilltop building” by Chris Devers is licensed with CC BY-NC-ND 2.0. To view a copy of this license, visit https://creativecommons.org/licenses/by-nc-nd/2.0/
In pipe robotics is the science of making robots that can inspect the inside of pipes. The cheapest way for companies to inspect their pipelines is to put a Pipeline Inspection Gauge, or PIG, because it is essentially a camera that can float down the pipe. They are uncontrollable though, and certain pipelines are difficult for them to traverse, if possible. Only around 0.5% of pipes cannot be inspected using PIGs, but these are mostly the pipes that are aboveground, and can cause huge environmental damage if they break. Some of these pipes that can’t be inspected through PIGs (unpiggable pipes) are nearing the end of their lives, and need to be replaced. What people are trying to do, though, is make a robot that can go through these obstacles.
Some of these obstacles are easier to think of a solution for, and some are harder. Squeezing past a valve is a fairly easy obstacle, but as PIGs are uncontrollable, they may get stuck on the valve with no way out. A change in diameter is another obstacle, if the diameter widens you may get a sharp drop that could damage the PIG if there isn’t much fluid in the pipe, and if the diameter shrinks, the PIG may slam against the wall and break. Vertical sections are another obstacle. If the fluid is going up, the PIG is heavy enough that it will just sit at the bottom, and if the fluid is going down the PIG might fall fairly fast, depending on how heavy it is, and break when it hits the bottom. Elbow bends are another obstacle, although easier. The PIG may be going fairly fast, hit the curving wall, and break. A T-section is one of the hardest obstacles as you may want to just go one way. The PIG is uncontrollable and can’t turn left or right, and may slam into the wall if going fast enough.
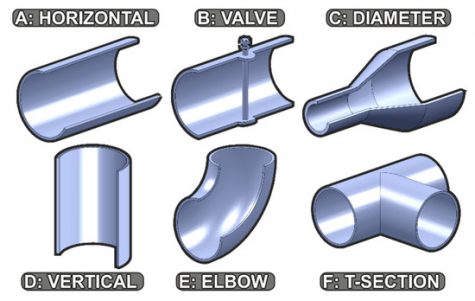
There are eight main designs that can navigate these pipes safely. There are wheels, treads/tracks, screws, snakes, inchworms, propellers, walking, and wall pressing. Wheeled robots have 4 or more wheels that they can use to drive down pipes that don’t have much fluid in them, or have been stopped up to let the robot inspect. Treaded robots have tracks that allow them to spread their weight over more surface area and hold heavier loads. Screw robots have a metal thread around the outside of the robot, just a a screw does, and can rotate to move forward and back down the pipe. Snake robots have joints and use them to slither through the the pipes. Inchworm robots press against the walls of the pipe in multiple places, just like an inchworm, and pull themselves forward and back. Propeller robots have propellers that allow them to move throughout pipes that are full of liquid without touching a wall. Walking robots use legs with multiple joints per leg and walk down the pipe.
The most common type of locomotion used in in-pipe robotics is the wheel method. Wheels are less bulky than treads, and can be used in combination with almost any other type of locomotion. They make up 43% of the robots being used, although most of these are not just wheels and use other methods as well. For example, you could have a robot that snakes along the pipe but has wheels to help it move. This would be considered both snake and wheeled.
Tracked robots are the next most common type. They are more bulky than wheeled systems, but they can carry a heavier load. They could have some equipment to work on the pipe while in it, or have an extendable rod with a camera in order to look down vertical sections. It could be combined with a caterpillar robot, and press against the walls but have tracks wherever it will press.
Screw robots are another kind of locomotion. The basic design is a metal thread, like a screw, wrapped around a central chassis. The robot could then rotate while pressing to the wall of the pipe in order to move forward and back. These robots don’t turn around corners very well, but if the corner is extremely shallow, they can manage a vertical pipe fairly easily.
Snake robots have multiple segments of their body that can twist and turn, allowing it to go around corners or go through changes in diameter. These robots are generally paired with a wheeled or tracked system so that it can move forward and back. These robots are not extremely common because they are generally fairly bulky because of all the motors for each segment.
Inchworm robots press against the wall in at least for places, two on each side, and pull the first point pressing the wall forward using motors, then the second, third, and fourth. These, just like the snake, aren’t very common because of the motors required to pull it forward. They are sometimes paired with wheel or track systems to pull it forward so that they don’t have to have as many motors.
Swimming robots are robots that have a propeller to pull them through the water. These can’t carry a very heavy load, but don’t have to touch the walls. These robots are very versatile, and are the only kind that don’t need wall-pressing, gravity, or magnetized means to stay where they need to be. They can have wall pressing, though, if they need some way to stop, by having something pop out and press against the wall just like an inchworm robot, or they can use electromagnets to stick to the wall.
Walking robots don’t have to have a huge surface area wherever they touch the pipe, and just walk forward on legs. These robots can be either gravitational or magnetic, but if you try to make them wall pressing you would have to increase the surface area of the “foot”. They are generally bulky for the same reason as the caterpillar and the snake, and therefore are not used very much.
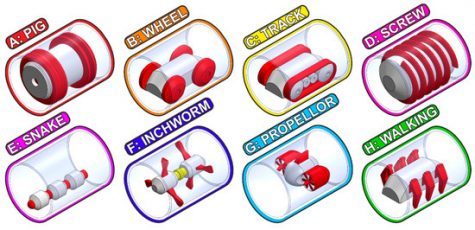
There are a few ways of making sure you stay where you want to be inside the pipe. Wall pressing, gravity, and magnets are the three main ways. They all have their advantages and disadvantages, and can be used in a variety of situations.
Wall pressing robots generate friction by pressing into the wall to stop themselves, and can have the main body of the robot in the center to measure the pipe diameter. They can only operate in a specific pipe diameter range, and one wall-pressing robot can’t even cope with a 20mm change in pipe diameter. Wall-pressing robots could be Wheeled, tracked, screwed, inchworm, snake, swimming, or walking. All inchworms, as of right now, are wall-pressing, but it is very commonly used in all designs.
Gravitational robots just use gravity to make sure they stay at the bottom of the pipe. These robots don’t have to have very much equipment on them, and generally find moving through smaller pipes is easier than some of the other robots. The kinds of robots that can be gravitational are wheeled robots, tracked robots, snake robots, or walking robots.
Magnetic robots have a magnet on one side that can keep them wherever they want to be, and they can stay at the top of the pipe to stay dry, and generally find going down vertical sections easier than the other kinds. Magnetic robots can be wheeled, tracked, snaked, swimming, or walking, but the main one used as magnetized is walking.
RELATED ARTICLES:
https://puretechltd.com/technology/purerobotics-pipeline-inspection-system/
https://www.deeptrekker.com/news/pipe-inspection-robots-all-you-need-know
https://www.sciencedirect.com/science/article/pii/S1877705814035218